Some people might think that Lead-Free Solders is the obvious choice because it contains no lead, is less toxic, and is more friendly to health. However, this idea is not necessarily accurate. While metallic lead does pose significant environmental and health risks — particularly when ingested — these concerns are more relevant to industrial settings, such as pollution from PCB manufacturing plants and occupational exposure of factory workers.[1] In fact, I believe that for electronics DIY hobbyists, choosing leaded solder is actually the wiser choice.
Metallic lead is indeed toxic and hazardous, but its harm is more reflected in the environmental damage it causes. Therefore, if a circuit board contains lead after production, care must be taken not to casually discard it into the natural environment. (Of course, even lead-free waste PCB or devices should not be disposed of carelessly; they should be collected and processed through specialized recycling methods.)
Additionally, my viewpoint is based on the perspective of an “amateur electronics enthusiast”. If you are engaged in long-term, frequent soldering work, that would be a different matter. However, for those who only do occasional soldering as a hobby, using leaded-solders is actually the “safer” choice. Why do I say this?
During the process of melting solder wire with a soldering iron and soldering ICs onto PCB, the primary harmful substances produced actually come from the fumes generated by the flux contained in the solder wire when heated. These fumes mainly contain the key components of the flux, including: formaldehyde gas, acidic gases, and halogen gases. These three types of gases are irritating and harmful to the human body.[2] These harmful gases mainly cause irritation to the respiratory tract and eyes.
So, as you can see, whether you use Lead-Base or Lead-Free Solders, always contains flux inside, which will release these gases and cause some level of irritation to our bodies. Therefore, regardless of which type of solder wire you use, as long as fumes are generated, it is important to ensure good ventilation and avoid inhaling the irritating solder smoke.
What about metallic lead? Does it form gases when heated, get inhaled, and absorbed by our bodies? The answer is: no.
The melting point of metallic lead is 327.2°C (621°F), and its boiling point is 1740°C (3164°F).[3] Meanwhile, the operating temperature of a soldering iron is usually around 300°C to 400°C. This working temperature is enough to melt lead but nowhere near high enough to vaporize it. Therefore, the fumes you can see, smell, and possibly inhale during soldering do not contain metallic lead, nor do they contain metallic tin, for the same reason.

Some might argue that while the operating temperature of a soldering iron is far below 1000°C, the range of 300 – 400°C is still sufficient to release PbO and ZnO₂ into the fumes. While ZnO₂ is relatively low in toxicity to humans, PbO can indeed be harmful. This argument is not incorrect — PbO can indeed float in the air as fine particles with the fumes.
However, there is a crucial premise: PbO must first be present. Although solder may contain lead (Pb), it does not automatically mean that Pb will oxidize into PbO when heated. In fact, even if you are using leaded solders, the working temperature is typically around 300°C, while the temperature of the molten metal usually does not exceed 300°C, and for PbO to form from lead, a temperature of at least 500°C is required.[4]
Since metallic lead is primarily absorbed through ingestion and inhalation, and does not significantly penetrate through skin contact, it is generally safe to use leaded solder as long as good practices are followed — such as minimizing direct contact, cleaning hands after handling solder wire, and ensuring adequate ventilation during soldering operations.
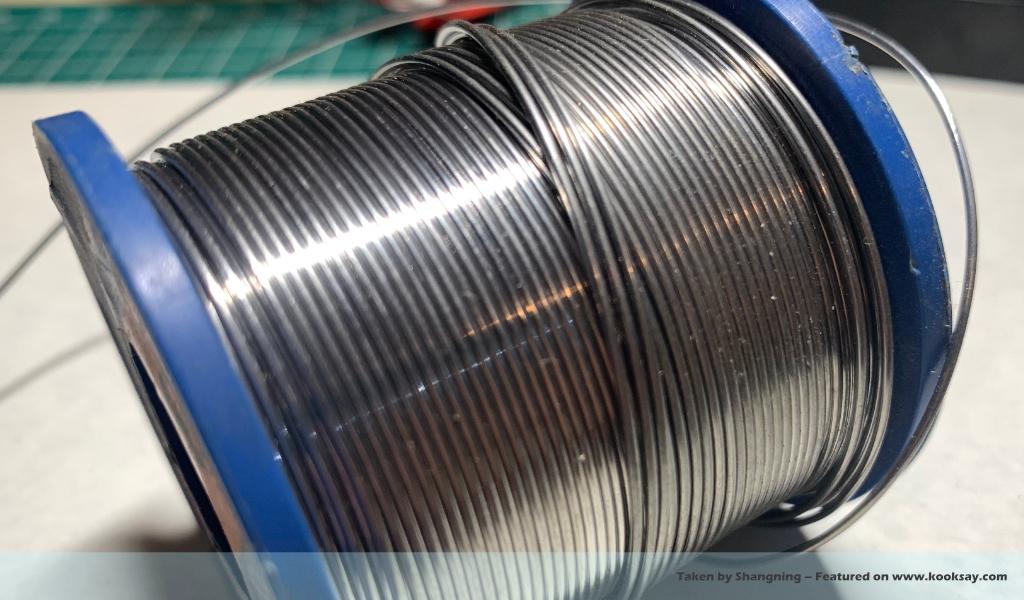
In summary, using leaded solder wire — due to its lower working temperature and better flow characteristics — shortens the time required for soldering and reduces the amount of fumes generated. Therefore, it is reasonable to conclude that the production of harmful gases during soldering is significantly lower, making the use of leaded solder a safer and more sensible choice.
Reference
- U.S. OSHA, Occupational Exposure to Lead, https://www.osha.gov/lead
- NIOSH. (1998). Controlling Health Hazards from Fluxes during Soldering. U.S. Department of Health and Human Services. https://www.cdc.gov/niosh/docs/98-116/
- CDC. (2005). NIOSH Pocket Guide to Chemical Hazards: Lead. https://www.cdc.gov/niosh/npg/npgd0368.html
- PubChem, Lead oxide Experimental Properties. https://pubchem.ncbi.nlm.nih.gov/compound/Lead-oxide#section=Melting-Point