When hand-soldering, the amount of solder wire and flux used should be kept to a minimum necessary amout.
Compared to the text-dominated internet era, the video era is more “emotional”. This emotionality stems not only from the visual directness of videos but also from the creative, sometimes irrational elements added to enhance entertainment value. These creative styles are often characteristic of humanities majors — imaginative, expressive, and highly engaging. However, such expressions can also lead to irrational misunderstandings — especially when beginners mimic what they see and fall into bad habits.
A common example involves videos of manual circuit soldering. To create visual impact, content creators often use excessive amounts of flux and solder wire. Their aim may be to impress viewers with a dramatic effect or to showcase their skill — demonstrating how they can swiftly remove large blobs of solder using techniques like drag soldering.
But in real-world soldering practices, whether it’s solder wire, solder paste, or flux, the usage should be kept to a minimum — just enough to get the job done. The flashy videos that use an excessive amount of soldering materials usually do so under very specific circumstances:
Using large amounts of flux, looking almost like Chinese cooking.
In proper soldering standards, this should generally be avoided. Flux is not a magical cure-all. It’s not the more, the better — nor can you use it recklessly. Flux can be corrosive and conductive. If not thoroughly cleaned, it may leave behind hidden risks. In formal soldering procedures, flux is best avoided when unnecessary and used only sparingly.
However, these “satisfying” videos aren’t entirely without value. The techniques shown are allowed under specific conditions in real-world soldering — especially in two scenarios:
- When reusing second-hand IC components or working with oxidized PCB pads;
- When dealing with high-density circuit designs that pack many ICs into a small PCB area.
In these cases, the increased use of flux helps reduce soldering difficulty at the cost of more post-cleaning work.
For example, in very compact circuit designs, ICs are often placed without enough spacing to ensure solder mask separation. High-density chips (such as those with only 0.5 mm pin spacing) are inherently difficult to solder by hand. Similarly, DIY enthusiasts often reuse ICs salvaged from old devices. In these “desperate” scenarios, using more flux can genuinely help solve difficult problems.
A proper amount of flux means: avoid it when possible; when necessary, apply it precisely using a 0.7 mm syringe, with the length matched to the width of the solder joint or pin header – Kooksay
Applying a large amount of solder to IC pins and then using drag soldering to remove the excess.
These “soldering satisfaction” clips might have originated in classrooms, where instructors demonstrate how to fix “bridging” (solder shorts between pins) if too much solder is applied. It could be a teaching tool, made dramatic to reassure students that such mistakes are fixable.
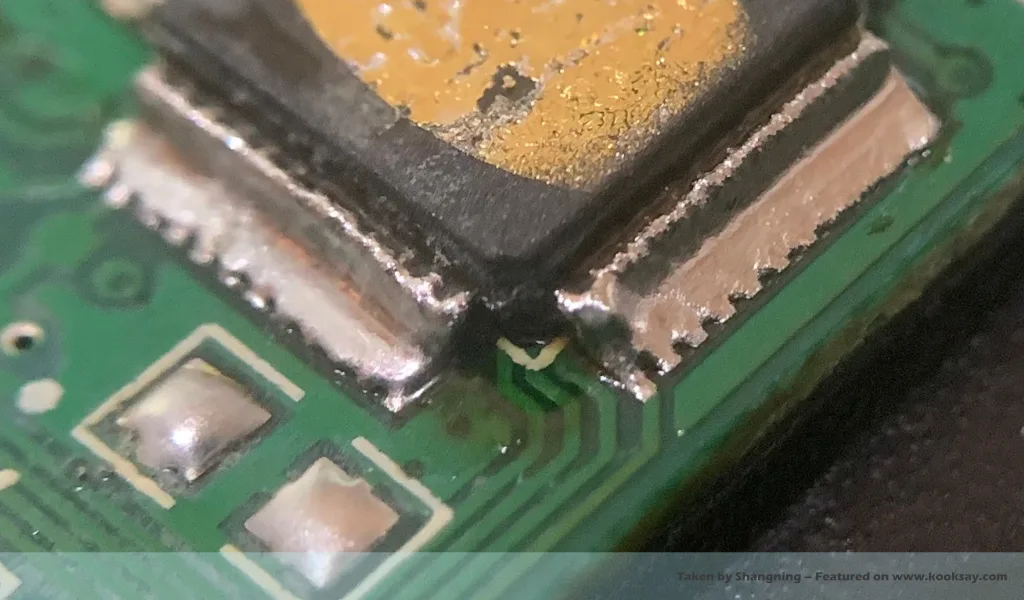
If you’re using drag soldering instead of point-by-point soldering, the correct and ideal outcome is this: as you drag the soldering iron across the pins, each one is soldered just right — no more, no less — and no bridging occurs. Drag soldering should not result in a giant bar of connected solder that you then need to fix.
Don’t chase speed — point-by-point soldering is the most reliable. If you must use drag soldering, aim for a clean one-pass result and avoid repeatedly dragging the solder – Kooksay
Solder paste should not be smeared across the whole board like spreading butter on toast.
This is another common video trope — spreading solder paste across the PCB instead of applying it dot by dot. The idea is to let surface tension during reflow pull the solder and ICs into place. Visually, it’s very satisfying and can be used to demonstrate physical concepts like “surface tension” and “self-alignment”.
But in actual production, this approach leads to numerous microscopic solder balls scattered around the board — ones that the naked eye can’t see. These tiny balls might not cause immediate problems and might not be cleaned off. However, over time, they can come loose due to vibration, move to unintended places, and pose serious electrical hazards.
When applying solder paste, don’t shy away from the tedious process — use a fine-tip syringe to place it dot by dot. Let go of the illusion that shortcuts will yield reliable results – Kooksay
Good-looking videos can provide enjoyable viewing experiences. But keep in mind: in real applications, we are cautious circuit builders — not flamboyant painters or wild chefs. Soldering is not just about technique; it is a combination of craftsmanship, aesthetics, and responsibility. Let’s enjoy the process — but never forget the discipline of engineering.