I once wrote an article recommending that electronics hobbyists use leaded solder wire. This opinion is far from unique — many discussions tend to favor leaded solder for DIY electronics due to its ease of use and ability to produce clean, reliable solder joints.
However, behind the general recommendation of using leaded solder lies a subtle detail that often goes unnoticed: the two most common formulations of leaded solder wire on the market are Sn/Pb = 63/37 and Sn/Pb = 60/40. Are these two types of solder really interchangeable?
This slight difference in composition is frequently overlooked, and it’s easy to assume they are effectively the same — perhaps just labeled differently due to slight variations in measurement. But the truth defies intuition: these two solder alloys have a fundamental and significant difference.
The 63/37 Sn/Pb solder forms a eutectic alloy, whereas the 60/40 Sn/Pb solder forms a non-eutectic alloy. Their physical properties are not the same.[1]
A eutectic alloy like 63/37 Sn/Pb has a sharp, well-defined melting point of 183°C. Below this temperature, it remains fully solid; once it hits 183°C, it transitions instantly from solid to liquid. Conversely, as it cools, the liquid metal solidifies just as rapidly when it drops below 183°C.
In contrast, the 60/40 Sn/Pb alloy is non-eutectic. Although it is still an alloy, it does not possess a single, distinct melting point. Instead, it has a melting range — from 183°C to about 190°C. When heated, partial melting begins at 183°C, but the solder doesn’t become fully liquid until it reaches 190°C. During this interval, the solder exists in a mixed state, with both solid and liquid phases.
This melting range creates an intermediate “plastic” state, where the solder is semi-solid and semi-liquid — soft and malleable, but lacking full fluidity.
With this understanding, it’s clear that 63/37 solder is the better choice for most leaded soldering applications. Its well-defined melting point means that once you see it melt, you can be sure it’s truly melted. In this fully liquid state, it has excellent flow and wetting characteristics, allowing it to form strong, reliable solder joints.
On the other hand, 60/40 solder can sometimes trick your eyes. It may appear to be fully melted, while in fact it hasn’t completely liquefied. If you attempt to solder during this misleading phase, the resulting joint may be imperfect — or worse, a cold or weak solder joint. This is especially problematic if a component shifts slightly during this plastic phase, as surface tension can tear the solder and compromise the joint.
So, shouldn’t 63/37 have already completely replaced 60/40?
Despite the differences, both alloys melt in a similar temperature range (183–190°C), and with a soldering iron set to around 260°C (even higher), you’re well above the melting point of either alloy. As a result, the practical experience of using them may not feel all that different.
However, from a manufacturing perspective, 60/40 solder has looser tolerance requirements. It doesn’t demand the ±0.1% composition precision needed for a eutectic mix, making quality control a bit easier and reducing production costs slightly.
Moreover, if a batch of solder deviates slightly from the 63/37 eutectic ratio but remains within acceptable performance limits, it might simply be relabeled and sold as 60/40. The purity of raw materials and the presence of trace impurities can also affect whether a batch qualifies as eutectic or not.
For these reasons, 60/40 solder isn’t going away. Both types continue to be manufactured and serve reliably in countless electronic circuits built by hobbyists and professionals alike.
That said, as a DIY electronics enthusiast, you don’t need to worry about the manufacturing side. What you should focus on is this: if you’re using 60/40 solder wire, avoid soldering or repositioning components during the cooling phase. Doing so can easily lead to poor joints or cold solder connections.
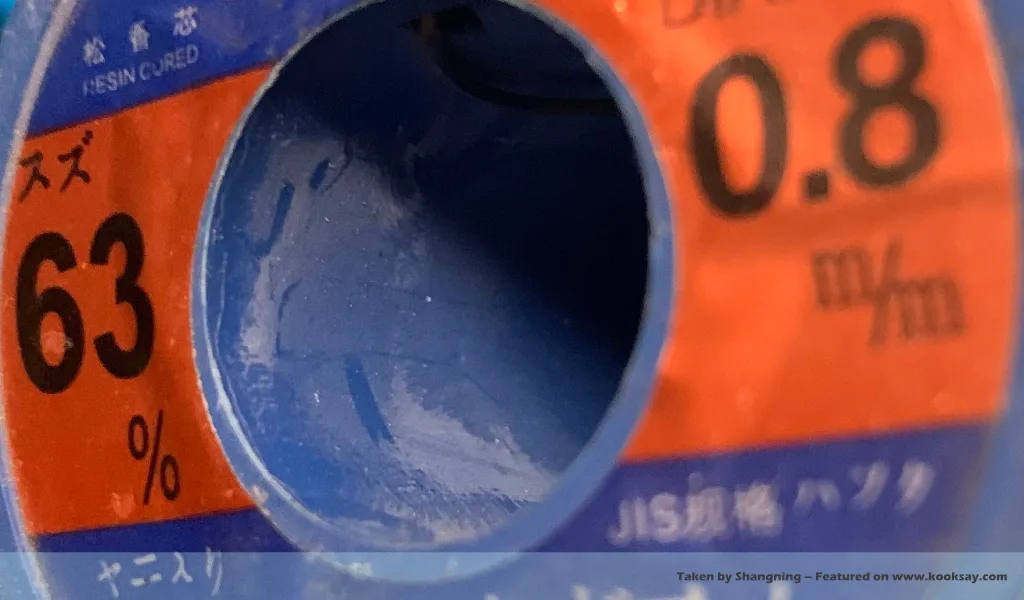
Feature / Property | 63/37 Sn/Pb (Eutectic) | 60/40 Sn/Pb (Non-Eutectic) |
---|---|---|
Eutectic Behavior | Yes (Eutectic Alloy) | No (Non-Eutectic Alloy) |
Exact Melting Point | 183°C (sharp transition from solid to liquid) | None; melting range: 183°C–190°C |
Melting Behavior | Instant full melting at 183°C | Partial melting starts at 183°C; fully melts at 190°C |
Plastic (Mushy) Range | None | Present; exists in semi-solid/semi-liquid state |
Visual Clarity of Melting | Easy to identify when fully melted | Can be misleading; may look melted but isn’t fully |
Risk of Cold/Weak Joints | Low (less likely to trap partially melted regions) | Higher (due to mushy state and possible component movement) |
Flow and Wetting Characteristics | Excellent once melted | Acceptable, but can be inconsistent during melting range |
Recommended for Beginners | Yes – easier to work with | Use with care – more sensitive to timing and movement |
Manufacturing Precision Required | High (±0.1% composition tolerance) | Lower; more forgiving in production |
Cost and Availability | Slightly higher production cost | Slightly cheaper and more widely produced |
References
- Wikipedia – “Solder alloys”, https://en.wikipedia.org/wiki/Solder_alloys